I am pleased to share a recent customer reference from my work as a simulation engineer. For Burnside Hydracyl Ltd. from Ireland, a reputable manufacturer of hydraulic cylinders for almost 50 years, I was asked to do a structural analysis on a hydraulic cylinder.
The customer
Burnside Hydracyl Ltd. from Ireland has been developing and manufacturing hydraulic cylinders in Ballymoon for over 50 years. The product range includes single-acting cylinders, double-acting cylinders and telescopic cylinders.
The challenge
A hydraulic cylinder is attached to a frame with a ribbed mounting plate welded to the side (Figure 1). The positions of the bolts are specified. The safety of this welded attachment must be verified.
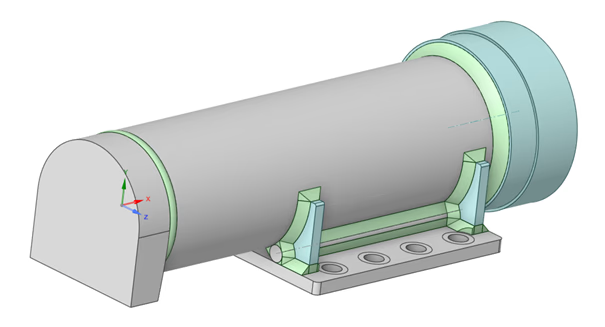
A number of 10,000 cycles with a single-stage collective is specified for the nominal load of the component.
The loads and boundary conditions
The geometry, loads and boundary conditions are half-symmetrical, so the model can be reduced to half. (Figure 2, left).
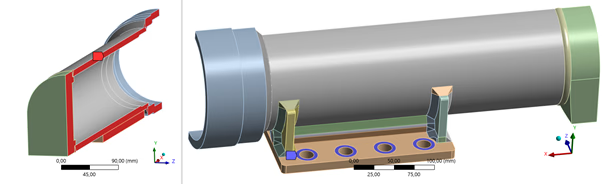
Despite the lack of geometric data for the frame and the specification of a rigid connection, a realistic simulation was created through conservative modelling with fixation at only 8 screws (Figure 2, right) and consideration of the oil pressure as a load.
The results
Deformation
The deformation is a maximum of 0.38 mm and is plausible (Figure 3). The deformation of the mounting plate was intentionally allowed.
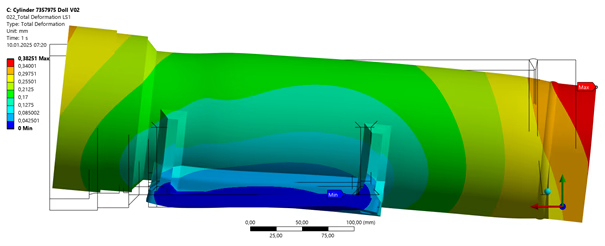
Stresses
The equivalent stresses shown in Figure 4 do not yet indicate whether the component is safely designed.
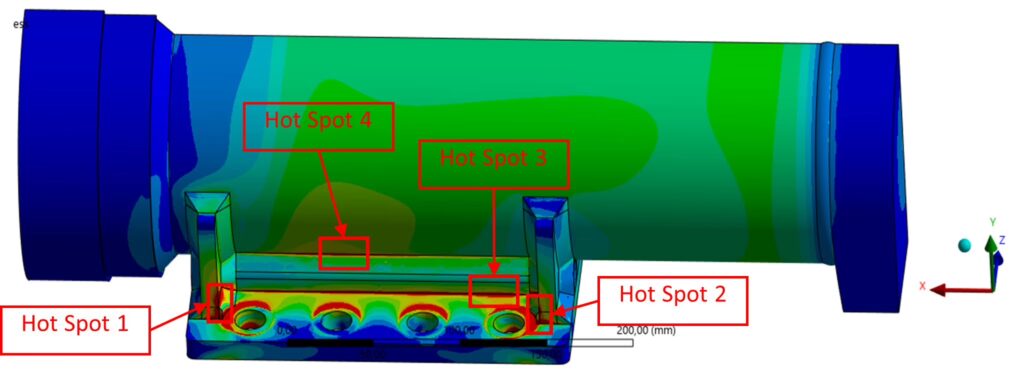
Assessment
The initial equivalent stresses were high, and the FKM guideline indicated a need for optimization at some hot spots. In particular, Hot Spot 1 had a static safety factor of 0.83, making optimization urgently necessary.

The optimisation
Geometry modification
The geometric adjustments were to be as minimal as possible, so it was proposed to extend the ribs slightly and design them with a smooth transition (Figure 5).
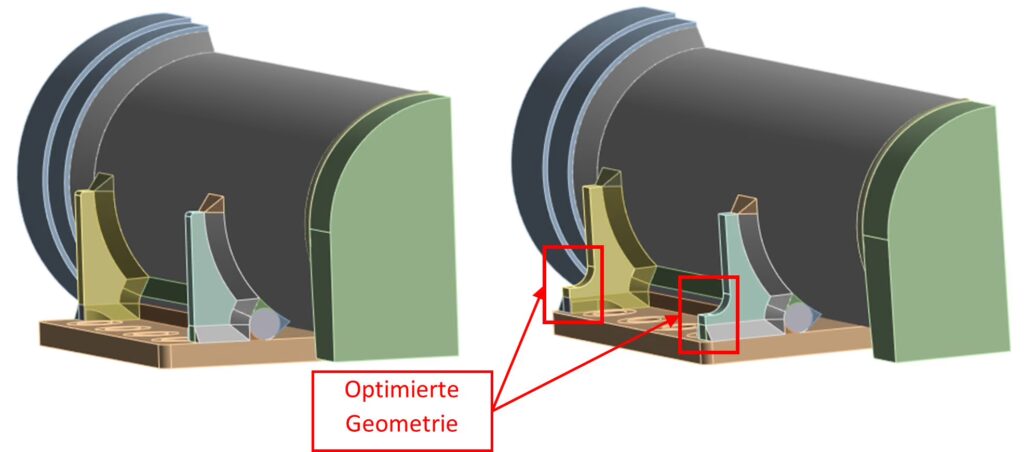
Stresses
Targeted geometric changes, such as extending the ribs with a smooth transition, reduced the deformation of the mounting plate and shifted the maximum stress to an unwelded radius. This can be seen in the same colour scale for the stresses, with a reduction in the red areas compared to the original calculation.
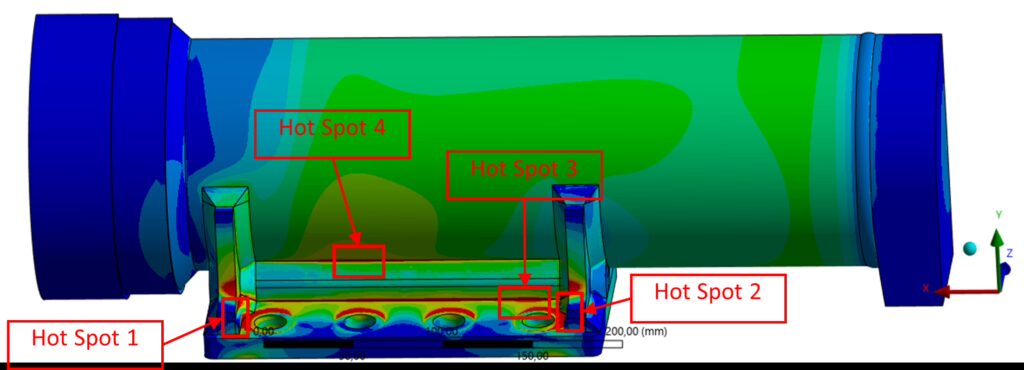
Assessment
The result speaks for itself: the stress level decreased significantly, and all hot spots now have a static and dynamic safety factor of over 1. The improvement in static safety at hot spot 1 was an impressive 48%!

Here is the improvement compared to the original geometry in percentage.

Conclusion
This case study impressively demonstrates how even small geometric changes, through precise simulation, can lead to a significant increase in component safety. This not only builds trust with the end customer but is also a valuable sales argument.
👉 Benötigen Sie schnelle, kosteneffiziente und zuverlässige Simulationsunterstützung für Ihre Projekte?
👉 Ich stehe Ihnen jederzeit gerne zur Verfügung. Besonders effizient ist die Zusammenarbeit, wenn wir uns bereits kennen und eine langfristige Partnerschaft anstreben.
#StructuralAnalysis #FEM #FEA #Simulation #HydraulicCylinders #MechanicalEngineering #Engineering #Design #ProductDevelopment #SafetyVerification #CustomerReference #CaseStudy #EngineeringServices #WeberSimulationEngineer